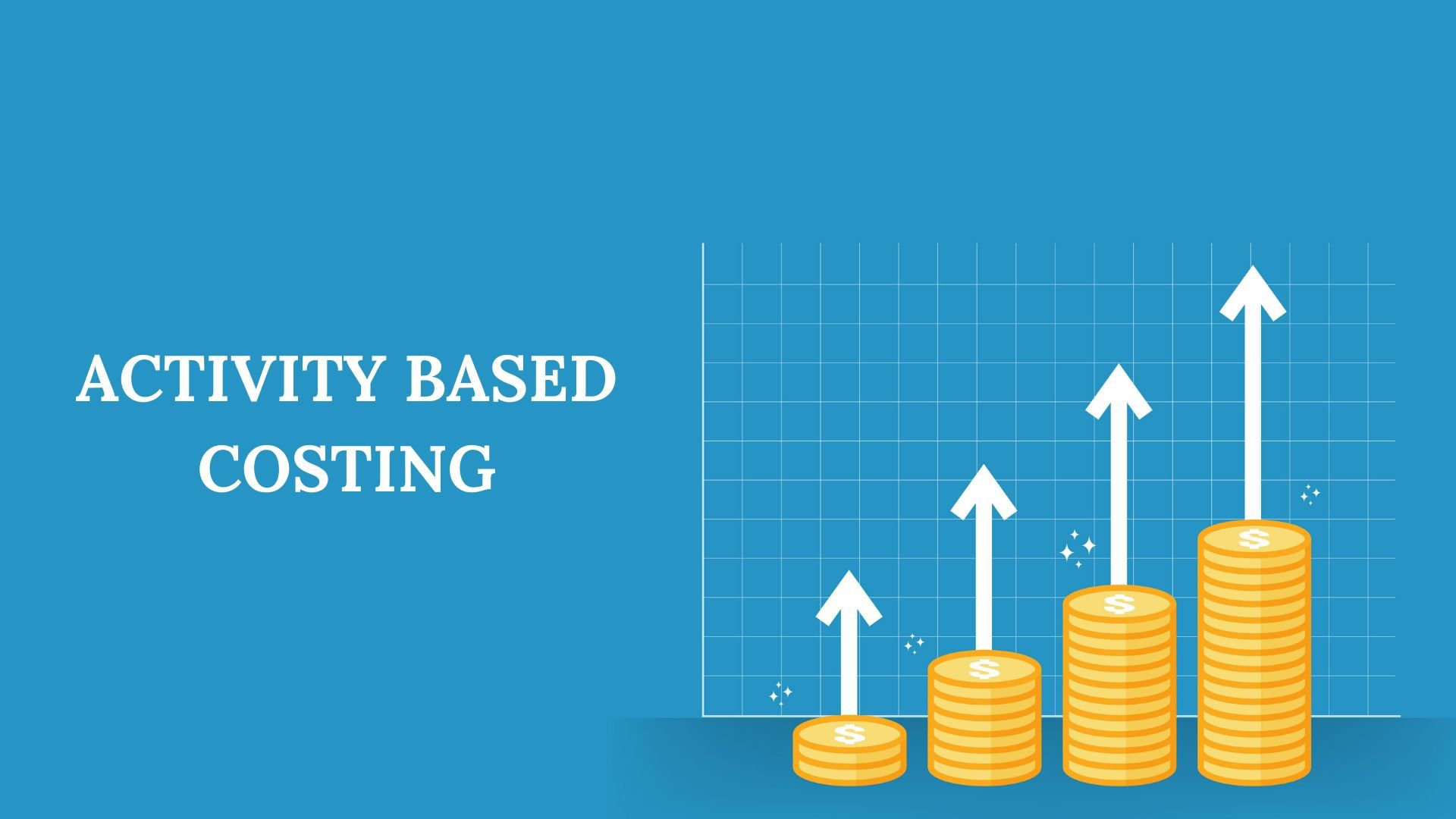
Activity-Based Costing | Uses, Advantages and Disadvantages | Marketing91
Activity-Based Costing | Uses, Advantages and Disadvantages
Definition
Activity-Based Costing is also referred to as ABC. It is defined as a costing method to identify activities in an organization and assign indirect and overhead costs to related products as well as services.
It acknowledges the relationship between costs, manufactured products and overhead activities.
Table of Contents
What is Activity-Based Costing?
Activity-Based Costing is recognized all over the world as an effective system. It provides valuable data that helps management to make informed business decisions.
Activity-Based Costing is used to a greater degree in the manufacturing industry as it helps to improve the reliability of cost data. It allows a firm to create viable pricing strategies that prove fruitful for them. This costing system is used in service pricing, customer profitability analysis, product line profitability analysis, product costing, and target costing.
Factors for Activity-Based Costing
Ensure the following critical factors for successful implementation of Activity Based Costing-
- Strong support from top management is essential for the successful implementation of Activity Based Costing. If managers are not in favour of the process, then it will become challenging to implement it in the company
- Until and unless some employees have in-depth knowledge about the organization’s operations, it will not be possible to implement the Activity Based Costing system successfully.
- Activity-Based Costing data will have to be linked to the evaluation of employees if you are looking to implement the system successfully. It is critical that employee evaluation is derived from Activity Based Costing data and not from any existing traditional costing system.
Advantages
The advantages of Activity Based Costing are as follows-
- Activity Based Costing helps the management to take quality decision by understanding the nature of each activity
- It helps to focus on value-adding activities and eliminating non-value-adding activities
- It assists in minimizing costs by offering information about the various opportunities that can reduce costs considerably
- It helps to understand the relationship between costs and its causes and thus can efficiently allocate realistic manufacturing costs for specific products in an organization
- It allocates manufacturing overheads to processes and products that use the activity accurately
- It helps to allocate cost to products correctly, and this results in a viable pricing policy
- It helps to determine product profit margins precisely
- It can compare the costs of each activity and thus find those that need to be improved or eliminated
- It gives accurate cost information. This is why management can easily adopt productivity improvement methods like BPR or Business Process Re-engineering and TQM or Total Quality Management
- It helps the management to fix the transfer price so that there are no issues while transferring the finished products from one department to another
- It identifies the cost drivers for all the activities, and thus it becomes easy to control the cost at its source
- It helps an organization in identifying profitable products, activities, services, projects, contracts, distribution channels, as well as customer segments.
- It uses numerous cost drivers to trace more overheads to the products
- It helps in a better decision-making process as the managers have reliable product cost data at their disposal
Disadvantages
The disadvantages of Activity Based Costing are as follows-
- It is not very feasible for small organizations.
- Reports from Activity Based Costing cannot be used for external reporting
- it cannot be applied if a company is producing only one or very few products
- Data produced by Activity Based Costing in some cases do not match with managerial performance standards that have been previously set by traditional costing methods
- It cannot be used to prepare a monthly profit statement
- It is challenging to install the Activity Based Costing across all facilities and product lines
- It is not easy to implement an Activity Based Costing system because of various difficulties like the selection of cost drivers, varying cost driver rates and assignment of typical costs
- It is of no use if a company has small overheads
- It is a time-consuming process and complicated because the method involves collection and preparation of data
- It is considered expensive as it costs more to collect and analyze information
- It uses a large number of cost pools, and this means unnecessary expenses for the company
- A large number of departments involved in the system increases the risk of data failure over time
- It requires several calculations for determining the cost of products. Even the cost rates have to be updated regularly. These measurements are expensive, and every firm cannot afford it.
Activity-Based Costing Process
The steps involved in Activity Based Costing process flow are –
1. Identifying activities
The first step of Activity Based Costing is to identify the critical activities involved in the production process through activity analysis.
It can include all sorts of activities like labour related, machine-related or support activities and in most cases include
- Batch level activities
- Unit-level activities
- Facility level activities
- Product level activities
2. Identifying and assigning costs
The next step of Activity Based Costing process flow involves identifying the costs that the organization wants to allocate. This step will help to save time later on as no one wants to waste time unnecessarily on specifics that are not relevant at that particular time.
3. Loading secondary cost pools
The next step involves creating cost pools concerning those costs that provide services to various other parts of the organization. It does not support the products and services of a company directly.
The secondary cost pools like administrative salaries, computer services etc. are afterwards allocated to other cost pools that have a direct relation to products and services. An organization can have several secondary cost pools based on the nature and allocation of costs
4. Loading primary cost pools
It is the time to create cost pools that are aligned with the production of goods and services. Most organizations prefer separate cost pools related to each product line.
It also creates cost pools for each facility or/and each distribution channel along with cost pools at the batch level to assign costs based on batch size.
5. Measure activity drivers
It can prove expensive to gather information about activity driver hence use already collected data. This will help allocate costs from secondary cost pools to primary cost pools as well as primary cost pools to cost objects.
6. Allocate costs
This step involves using activity drivers to assign costs in the secondary cost pools to primary cost pools
7. Charging costs to cost objects
Organizations use activity drivers for allocating primary cost pool-related content to cost objects. Assign separate activity driver for every cost pool. Allocating the cost is manageable.
Just take the total cost of each cost pool and divide it by the overall activity in the activity driver. This will tell you the cost per unit of the relevant activity. You can now allocate the cost per unit to the cost objects based on the usage by the activity driver.
8. Put together reports
This step will help to convert the results that you have derived from the Activity Based Costing process into reports. These are specially meant for the management and will provide a full cost view of the results.
9. Acting on the available information
After viewing the Activity Based Costing report, the first thing the managers do is minimize the number of activity drivers that were previously used by every cost object to reduce overhead costs.
Uses
The uses of Activity Based Costing are as follows-
1. Customer profitability
Activity Based Costing is used to sort through the additional overhead costs and determine which of the customers are earning profits. This helps the management to pay special attention to the customers who are its largest profit generators and turning away the ones that are considered its unprofitable customers.
2. Activity costs
Activity Based Costing is a system that is used to track the cost of activities. It is also used as a feedback tool to measure the ongoing cost of a specific service.
Activity Based Costing is used to drop unprofitable channels and lower distribution costs
4. Manufacturing or outsourcing
It is a dilemma for an organization whether to manufacture a product by itself or outsource it from another party. Activity Based Costing offers a detailed view of the cost related to in-house manufacturing.
It is used by the company to understand whether it will be profitable to make the product or purchase it from another party.
5. Determine margins
Activity Based Costing is used to determine the margins of product lines, products and subsidiaries.
6. Minimum price
Activity Based Costing is used to determine the overhead costs that should be included in the minimum cost so that the product price remains minimum
7. Production facility cost
Activity Based Costing is used to sort overhead costs at the plant itself. It becomes easy for managers to compare production costs between different facilities.
Conclusion
Activity Based Costing is an accounting method of costing that is used to find the total cost of activities that are required to make a product. Pricing products is essential for an organization, and it is an Activity Based Costing method that helps in making accurate assumptions about the various offerings.
It is a methodology that works best in a complex environment where it is not easy to sort out tangled processes.