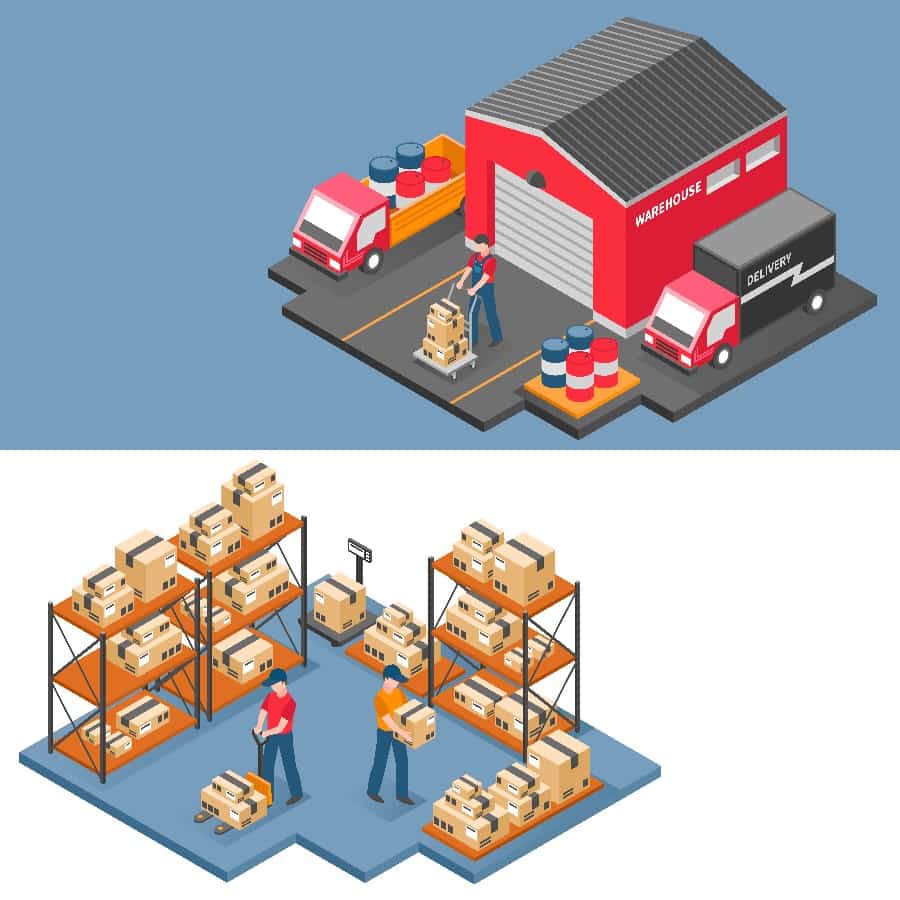
Inventory Costs Definition - Meaning, Types And Methods | Marketing91
Inventory Costs Definition – Meaning, Types And Methods
Inventory Cost includes all the costs associated with the management, storage and procurement of inventory and is a necessary calculation for all businesses. Inventory cost also includes the costs for storage facilities, insurance pilferage, handling, depreciation, breakage, taxes, obsolescence and the opportunity cost of capital.
Table of Contents
What are the inventory costs?
Inventory cost is often defined as the percentage of the inventory value yearly. Assessing expenses related to inventory is essential because if not correctly done, it can have repercussions on the management as well as the finances of an entity.
The inventory cost is useful because it determines the amount of profit that can be made on the inventory, where the firm can make viable changes, how can it reduce costs successfully, how can the capital be allocated and which products or suppliers to choose for the benefit of the organization.
A significant portion of the total assets of an organization is represented by inventory and a reduction in its level has a direct impact on the profitability of a business entity. It is a fact that high holding costs favor low inventory level and needs frequent replenishment.
The cost of inventory is high and it is essential to keep a check on it; otherwise, it can have a substantial impact on the cash flow by eating into the profits. Find the right balance if the business is looking for long-term success.
Types of inventory costs
It is a myth that regular accounting will provide an exact estimate if the inventory costs. It is not possible to keep track of all the costs or allocate them properly but to get a better idea of the inventory cost you will first have to know what types of costs are associated with it. The different types of inventory costs are as follows-
1) Ordering cost of inventory
The ordering cost of the inventory occurs whenever an order for inventory is placed. It is also referred to as setup costs and includes
- Receiving costs – The receiving costs are those expenses that incur when goods are unloaded at the warehouse and inspected to see that they are the correct items or the ones that were ordered and are free of any defect
- Clerical costs of preparing purchase orders – As the name suggests it refers to various clerical costs for instance communication costs, accounting, invoice processing
- Cost of electronic data interchange ( EDI )– It is a system that is used by large businesses to minimize the ordering process costs.
- Transportation costs – The transportation costs are those expenses that are incurred while moving or transporting goods from one place to another, for instance, to the outlet or the warehouse. It is variable to a higher degree and is dependent on items and industries.
- Cost of finding suppliers and expediting orders – These are essential costs for the business and are generally inconsistent.
No matter how small or big an order is, you have to incur an ordering cost. The total amount increases with the number of orders placed. The overall ordering cost can be minimized by placing a large blanket order for an extended period and issuing releases against them as needed.
Ordering cost is inversely related to carrying cost of inventory because low carrying cost means high ordering cost and vice-versa. A business entity willingly tolerates high ordering costs if it results in low inventory carrying costs. It is the responsibility of the organization to keep a watch on its ordering as well as moving costs to maintain a balance in order sizes and ultimately minimize overall costs.
Ordering costs are included in the overhead cost pool and are allocated to the units produced in every period.
2) Carrying cost of inventory
Carrying costs of inventory refers to the expenses that incur for inventory storage and its maintenance. It is also known as holding costs because of its nature of maintaining the inventory for the interim period. The carrying costs of inventory before it is sold typically includes
- Storage space costs – The storage space costs incur when the inventory is stored in a place. It is never fixed because space can vary by location. The inventory costs include the cost of storage facility, facility maintenance costs that include ventilation, heating and lighting, lease payments, property tax, and depreciation.
- Inventory risk costs – The inventory risk cost is associated with the loss of goods that can incur because of several reasons, for instance, damage in transit, shipping error, vendor fraud or theft.
- Inventory service costs – The inventory service costs are the costs that incur in the physical handling of the goods. It also includes costs related to cycle counting and inventory control, security, insurance, IT hardware and applications if used.
- The opportunity cost of the money invested in inventory – This type of inventory costs can be derived by looking at the lost alternatives that have tied up cash in inventory for instance investments in mutual funds or term deposits
- Inventory financing costs – Inventory financing costs are complex by nature and are dependent upon the type of business an entity is involved in. These types of inventory costs are related to the investments made in the name of inventory and include costs like interest on working capital.
The carrying cost of inventory is related to managing inventory, either in-house or via third-party service providers and outsourced vendors.
Carrying costs are included in the overhead cost pool and allocated to the number of units that have been produced in every period
3) Shortage of stockout costs
The shortage costs refer to the situation when a business is out of the stock for whatever the reason. It is also known as stock-out costs because of its nature. Some of the shortage costs are
- Emergency shipments – This type of costs incurs when you have to pay an additional sum to change suppliers or to get delivery on time so that the goods reach their destination without hassles
- Disrupted production – Some business entities are involved with the production and selling of products. Shortage of stock-out costs for such entities means paying for things for instance factory workers who are sitting idle even during the times when the factory is manufacturing nothing.
- Customer loyalty and reputation – if the customer is unhappy, it will be reflected via their shift in allegiance and loyalty. This will lead to loss of business as the customers will try to find greener pastures that suit them better and the company will take a hit in terms o customer loyalty
When the demand exceeds the supply of the inventory that is available to the business entity, then the shortage costs will incur. Internal issues, market shortage and late supplier lead times are some essential reasons for shortage costs
Types of inventory costing method
The various inventory cost methods are as follows-
1) First in, first out
This method of inventory costing is also referred to as the original purchase method because of the way it operates. The assumption in this method is that the goods that have been purchased at first are the ones that will be sold first and so on
The first in first out method ensures that no profit or loss occurs on this account. This is the best system when the product prices are stable, but what happens during adverse or unstable conditions. During a period of inflation, the operating statement will reflect inventory profits and during deflation, it will show a narrowing of profits.
Both GAAP and IFRS accept the FIFO or first in first out method and it becomes the right choice for brands that are considering overseas or global expansion.
2) Last in last out
The last in last out is one of the significant methods for inventory costing and is also referred to as the replacement cost method. This method is based on the assumption that the goods which are sold are the ones that have been purchased last or most recently. It is merely a reversed method of first in first out method that emphasizes on everything first.
The best part of the last in last out method of inventory costing is that it tries to level the profit as well as loss during both deflation and inflation periods. This is because the materials are issued at cost and they relate to the current price levels closely as possible. It can maintain the real capital intact. This is why the new requisitions lower the profit margin because of high costs during inflation and during deflation, the fall of profit margin is minimized due to the low cost of the last unit that an entity has purchased.
The organizations that deal with perishable products do not follow the LIFO or last in last out method of inventory costing because it does not reflect the actual flow stock. The GAAP accepts LIFO but IFRS does not accept it as an approved accounting method of inventory costing. This is because bookkeeping is a bit difficult with LIFO and as the cost of goods sold is high, it can result in the low-profit margin and lower income taxes.
3) Special identification
Organizations that assigns a unit cost to every single unit uses the specific identification inventory cost method. The amount is applied to the accounting records after the sale of every item. As the cost of goods sold will fluctuate depending upon the shipping, production and other relevant costs that change over time, the unit cost of every unit will automatically vary.
This method is used for expensive and exclusive products for instance artwork, boats, fine jewelry, luxury cars, etc. The organization has to keep a detail-oriented and diligent record-keeping in this method.
4) The average inventory cost method
The average inventory cost method is a middle ground of both FIFO and LIFO methods. It does not use the first-recorded or the last-recorded prices but takes out the average unit cost for its calculations. It can be subdivided into
- Weighted average inventory cost – In the weighted average inventory cost method, the business entity has to make proper calculations at the time of every purchase. To minimize or eliminate the effect of earlier prices that were incurred, it considers both the total costs and total quantities.
- Simple average inventory cost – In the simple average inventory cost method, the materials are not charged at actual cost. The method of calculation is different as it wants to determine the approximate figure by dividing the total of the prices by the number of rates which may lead to either profit or loss.
- Periodic weighted average inventory cost – In the periodic weighted average inventory cost method calculations are made at the end of the period by dividing the total cost of purchase by the total quantities purchased. It is considered a better option because it includes both overall cost and total amounts.
- Periodic simple average inventory cost – In the periodic simple average inventory cost method the issue price is calculated at the end of a given period by dividing the total material price by the number of prices periodically
5) Base stock inventory costing method
This method has several similarities with the FIFO inventory costing method along with some additions and modifications. It takes into account the fixed minimum quantity of stock that has to be maintained regularly and should be carried forward at the actual cost at the end of every fiscal year.
Most organizations have a minimum stock inventory in store which is released at the time of an emergency. The base stock inventory costing method is mostly used in industries that have to use a variety of raw materials. The technique helps to lessen violent and sudden fluctuations in the gross profit.